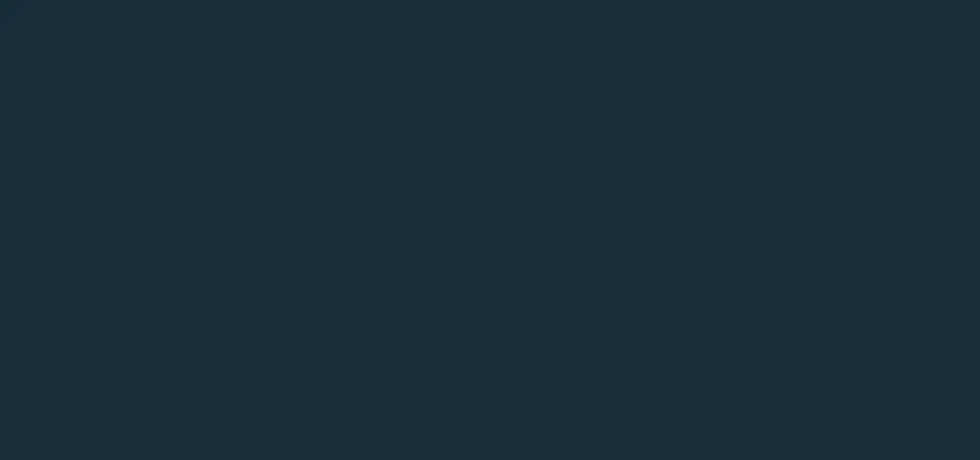.webp)
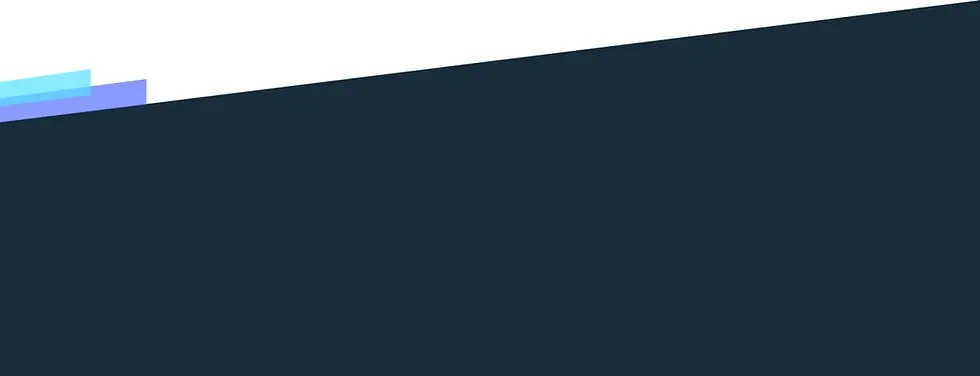.webp)
Challenges Addressed
Inconsistent Quality Control: The manual inspection process was prone to inconsistencies and human errors, which sometimes allowed defective products to enter the market. Quality control teams struggled to keep pace with the high production rates, which occasionally led to oversight in the quality check process.
High Production Costs: Due to recurring quality issues, the manufacturer faced costly reworks and returns. The reliance on human inspectors was no longer sufficient to maintain the high standards demanded by the market, further escalating operational expenses.
Lack of Real-Time Monitoring: Without real-time feedback, product defects were often identified late in the production cycle, delaying corrective measures. The inability to address quality issues as they occurred negatively impacted overall production efficiency.
Inadequate Data Utilization: The manufacturer struggled with the ineffective use of data collected during the production process. Although various data points were recorded, there was no systematic approach to analyze this information for quality improvement.
NEXA's Approach
NEXA developed a sophisticated embedded vision solution that integrated advanced imaging technology directly into the production line, enabling automated, real-time product inspections that significantly enhanced the accuracy and speed of quality checks. This fully automated system effectively identifies defects such as scratches, misalignments, and color inconsistencies without human intervention. Continuous real-time monitoring ensures that any detected defects trigger immediate corrective actions, while state-of-the-art image processing algorithms analyze product images to guarantee fast and precise detection of potential issues.


Manufacturing Product Production Quality Check through Embedded Vision
Client Spotlight
A leading electronics manufacturer faced significant challenges in maintaining consistent product quality across its production line. With a diverse portfolio of products and rigorous quality standards, the company sought a solution to automate its inspection processes, thereby reducing human error and boosting production efficiency. They partnered with NEXA to develop an embedded vision system tailored to their specific needs, ensuring high-quality products across the board.
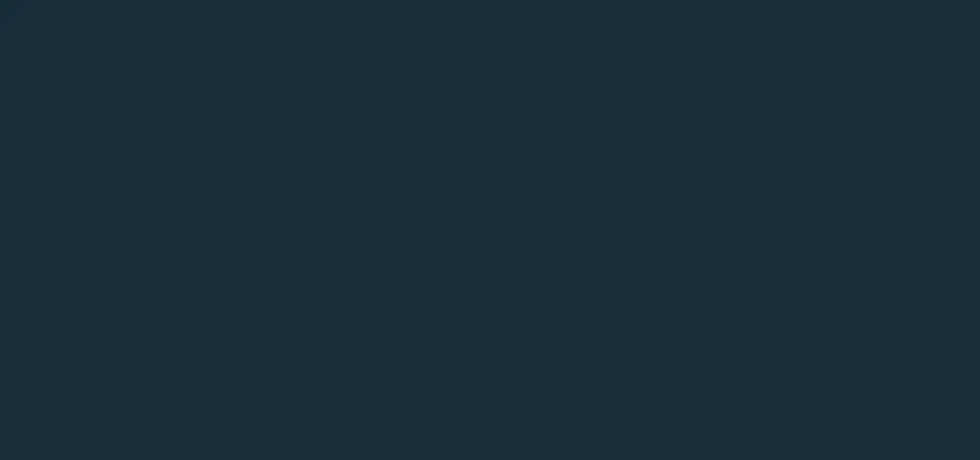.webp)
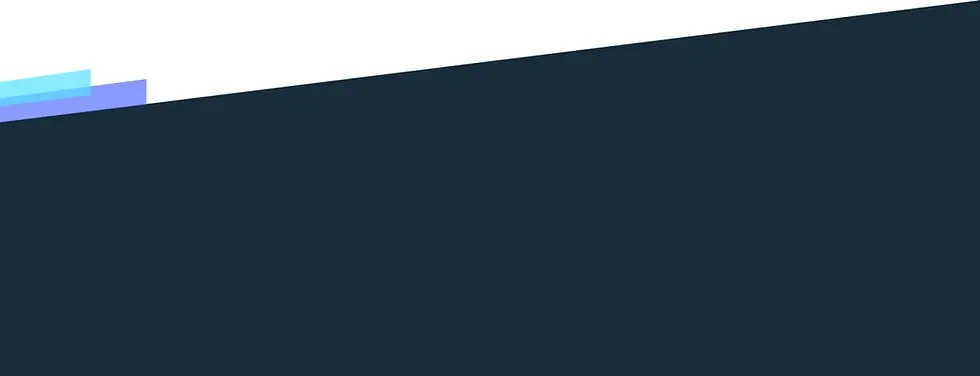.webp)
Results Achieved
Improved Quality Assurance:
The embedded vision system significantly improved the consistency and accuracy of product inspections, leading to a 40% reduction in product defects. As a result, the manufacturer delivered higher-quality products to the market.
Cost Savings:
With fewer defects, the need for rework and returns dropped substantially, contributing to a 25% reduction in production costs related to quality issues. Consequently, the combination of improved product quality and decreased costs fostered a more sustainable production environment, positively impacting the company's bottom line and reputation in the market.
Real-Time Monitoring:
The embedded vision system enabled real-time quality monitoring, allowing the production team to address defects immediately, reducing downtime, and optimizing production efficiency.
Enhanced Data Insights:
The system provided valuable insights into production quality trends, helping the client make informed decisions on process improvements and resource allocation. The ability to track quality trends in real-time also supported strategic decision-making, empowering management to make data-driven choices regarding product enhancements and operational efficiency initiatives.
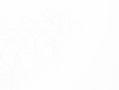
Implementation
Requirements Gathering: NEXA’s team worked closely with the client’s quality control and production departments to understand the critical pain points and define the quality benchmarks that needed to be met by the embedded vision system.
System Design: The solution was designed with modularity and scalability in mind. High-resolution cameras were placed strategically throughout the production line to capture detailed product images at key stages of production.
Image Processing Algorithms: Advanced image processing technology was implemented, enabling the system to detect a wide range of defects with precision, from surface imperfections to structural misalignments.
Testing and Calibration: The system underwent thorough testing and calibration to ensure its reliability. NEXA incorporated feedback from the client’s quality control team to fine-tune the system and maximize its usability.
Deployment and Training: Once testing was successfully completed, the system was deployed across the production line. NEXA provided comprehensive training to ensure the client’s staff could fully leverage the system’s capabilities. performance. Adjustments were made to meet client expectations, enhancing usability and efficiency.